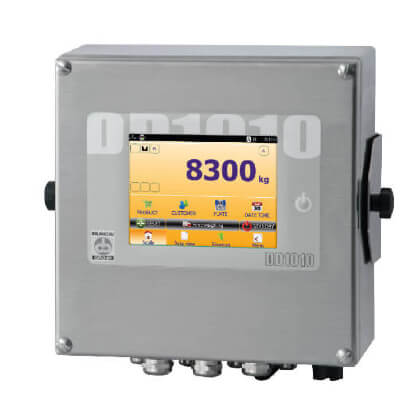
Weight measurement is a crucial process in a vast array of sectors, ranging from industrial manufacturing to agricultural operations. The need for precise, consistent, and reliable readings cannot be overstated, especially when daily business activities depend on accurate data. Amidst the many components that make up a weighing system, the device that often takes center stage is responsible for capturing, interpreting, and displaying load information. This vital piece of technology is typically referred to as a weight indicator, and it seamlessly bridges the gap between sensor signals and a clear readout.
Over time, weight indicators have evolved to offer advanced features such as digital displays, user-friendly interfaces, and the ability to store historical measurements. The result is a solution that modernizes workflows and ensures greater transparency throughout the weighing process. Understanding how a weight indicator works, what variations exist, and where these devices are employed can help businesses make informed decisions related to the efficiency and reliability of their weighing equipment.
Understanding the Basic Function
A weight indicator is often the brains behind a weighing system. It connects to the load cells that sense tension or compression, converting those analog signals into digital data that can be understood by users. In simpler terms, load cells pick up minute variations in voltage or resistance when a mass is placed upon the scale. The weight indicator receives that signal and translates it into a unit of measurement, typically kilogram or pound, that an operator can read instantly on the device’s screen.
One of the key benefits of a weight indicator is its ability to eliminate guesswork and present data in a simple, easy-to-read format. Rather than requiring users to calculate load by comparing mechanical dial positions, the indicator shows precise figures with minimal or no margin for human error. In many modern weight indicators, there are also alarms or thresholds that can be programmed to alert operators when a certain maximum or minimum limit is reached. This feature is especially relevant in processes that demand tight tolerances, such as batching, filling, or grading.
Accuracy is upheld through periodic calibration, and many indicators come with self-diagnostic tools to ensure that readings remain consistent over time. Some advanced models are also capable of transferring data to a central system or uploading figures to a cloud repository. This functionality can be critical in environments where traceability and quality assurance are paramount. By taking advantage of these features, businesses can reduce manual documentation, lower the risk of measurement errors, and improve overall workflow efficiency.
Types of Weight Indicators and Their Features
There are several types of weight indicators currently available, each one developed to suit distinct operational requirements. Basic digital indicators present straightforward readings and might include features such as a backlit LCD screen and simple keypad programming. These types of indicators are typically suitable for smaller environments, including grocery stores or medical clinics, where weighing tasks occur on a less complex scale.
On the other end of the spectrum, there are advanced programmable indicators that can be integrated into automated processes. These can store product IDs, run batch operations, and even control external devices such as relays or sensors. By incorporating programmable logic into the indicator, businesses can achieve more streamlined operations. For example, a packaging facility might automatically stop a conveyor belt the moment a bag has been filled to the exact target weight, preventing overfills and product wastage.
Many modern weight indicators also offer connectivity options for data collection and monitoring. It is increasingly common for units to come equipped with ports such as RS-232 or USB, or even wireless communications using Bluetooth or Wi-Fi. This added connectivity makes it easier to track and analyze weight readings over time, integrate them with enterprise resource planning systems, or generate real-time performance dashboards. The ability to transform raw scale data into actionable business insights demonstrates just how pivotal a weight indicator can be in driving operational improvements.
Applications Across Different Industries
Weight indicators play a vital role in paving the way for productive and efficient operations in numerous fields. In the logistics and warehousing sector, for instance, they help ensure that shipments meet weight limits and comply with regulatory standards. Having accurate knowledge of load sizes can save transport companies from incurring fines, reduce the risk of overloading, and streamline fleet management.
In the food and beverage industry, weight indicators are used in portioning, batching, and quality control. Whether measuring out ingredients in a bakery or confirming that canned products maintain a uniform fill level, these devices facilitate consistency and compliance. The near-instant feedback that an indicator provides means that adjustments can be made quickly if discrepancies arise, helping to preserve product quality and maintain customer satisfaction.
Outside of manufacturing and logistics, weight indicators are commonly used in the agricultural sector and in healthcare settings. Farmers rely on them for measuring livestock feed, monitoring growth patterns, and overseeing harvest yields. Healthcare facilities employ medical-grade indicators for patient care, ensuring that weight data is both accurate and traceable. Regardless of the specific industry, the underpinning purpose remains consistent: a weight indicator supplies critical measurement data that drives informed decision-making and fosters operational efficiency.
Conclusion
A weight indicator serves as a vital link between raw sensor data and the valuable insights required for countless day-to-day applications. Through the use of precise electronics, user-friendly interfaces, and effortless integration features, they create a solid foundation for reliable measurements that businesses can trust. By selecting the right device for specific operational needs, companies can enhance production flows and uphold stringent quality requirements.
If you are interested in discovering more about advanced weighing solutions and enhancing your business operations, feel free to explore our extensive range of systems and scales. You can browse our offerings for both general-purpose and specialized equipment, ensuring that your weighing processes are as robust and accurate as possible.