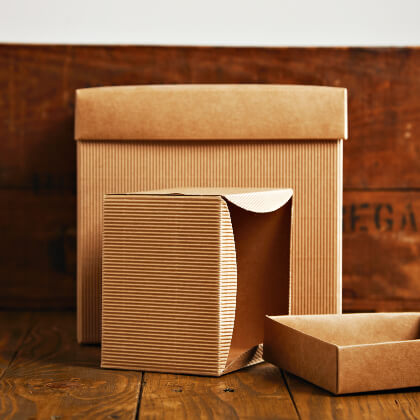
In modern production lines where goods require swift yet reliable preparation for shipment, accurate measurement systems are essential. These systems determine the correct quantity of product that goes into each container, helping businesses reduce waste and comply with industry standards. Selecting the right measurement methods involves assessing vital factors such as the nature of the goods, packaging requirements, and necessary precision levels.
At Sasco Africa, our team recognizes the necessity of dependable weighing solutions to match a wide range of packaging needs. Whether companies deal with small-scale consumer goods or bulk industrial materials, reliable measurement technology can help maintain consistency. It also avoids costly product returns or negative customer experiences related to inaccurate weights. By understanding how various tools work and interact with other production processes, businesses can optimize every step of their packaging workflow.
Types of Weighing Equipment in Packaging
Weighing devices used during the packaging process come in different forms, each offering specific advantages for different operational needs. One of the simplest examples is the bench scale, often used for smaller parcels and items. Bench scales are known for their user-friendly interfaces and relatively small footprint, making them suitable for use in workstations where employees can quickly verify weights. For heavier or bulk shipments, businesses often rely on floor scales that can handle substantial loads. In both cases, the aim is to provide fast, reliable weight readings that meet accuracy requirements for commercial transactions.
Another type is the checkweigher, which is integrated directly into a conveyor belt system. This dynamic weighing solution ensures that each product passing through meets a precise weight range. If an item falls outside the designated tolerance, it is automatically rejected from the line. This setup is vital in industries such as food and pharmaceuticals, where consistent weight is crucial for both consumer safety and compliance with regulations. Checkweighers may also collect data that can be analyzed to identify trends or recurring issues, helping managers address bottlenecks or reduce product waste.
Load cells are at the core of many packaging scale designs. These sensors convert the force of an item’s weight into an electrical signal, allowing the system to interpret and display the correct measurement. Because load cells can vary in capacity and configuration, they are found in everything from small electronic scales to large industrial weighing platforms. By choosing the right type of load cell and pairing it with a robust indicator, businesses can customize weighing operations to achieve optimal performance under specific environmental conditions, such as high humidity or extreme temperatures.
How Precision Scales Enhance Packaging Efficiency
Precision scales contribute significantly to the overall efficiency of packaging lines. Business owners and operators depend on these devices for their speed and accuracy in determining how much product is placed into each box or bag. By using systems that deliver exact weight data, companies not only avoid discrepancies that may lead to overfills or underfills, but they also foster better consumer trust. When goods are properly weighed, end-users experience consistent packaging content, and this consistency encourages brand loyalty over time.
A critical advantage of using high-accuracy weighing instruments is their ability to minimize waste. Overfilled products can translate into profit losses, as companies unwittingly give away more product than is needed to meet labeled weights. On the other hand, underfills can hurt a company’s reputation and lead to product returns or potential legal issues over mislabeled weights. Precision scales help maintain a fine balance, allowing businesses to maximize material utilization without sacrificing regulatory compliance and consumer satisfaction.
Moreover, integrating advanced scales with data collection software fosters operational insight. Operators can track trends in weight inconsistencies and take corrective action much earlier. Anomalies, such as repeated underweight packages, signal potential machine malfunctions or improper line setup. By catching these issues at an early stage, rework can be reduced, and throughput can improve. This, in turn, makes packaging lines more cost-efficient and agile in response to changing market demands, directly impacting a company’s bottom line.
Integrating Weighing with Broader Operational Systems
Modern packaging environments rely heavily on seamless integration between weighing machines and other production technologies. Enterprise Resource Planning (ERP) systems, for instance, can collect crucial weight data in real time, feeding updated inventories and production forecasts. This eliminates guesswork and allows businesses to keep tighter control over stock levels. When a particular line experiences a sudden uptick in output, managers can reallocate resources based on real data, ensuring the right materials and labor are available to meet demand.
Automation is another key topic when discussing comprehensive system integration. By linking scales to automated conveying systems, robotic arms, and labeling machines, producers can accelerate the packing process significantly. After each item is weighed, it can be guided to the next phase, where it can be sealed, labeled, and prepared for shipment. The precise weight information helps to generate accurate shipping labels, particularly critical for freight costing or regulatory compliance. This improved level of coordination has a positive ripple effect on the entire shipping pipeline.
Regulatory compliance can also be simplified with integrated weighing setups. When inspectors request product weight data, having a centralized database that continuously receives input from each scale guarantees the data is consistent and readily verifiable. This streamlined data reporting is indispensable in industries where traceability requirements are stringent, such as food processing or pharmaceuticals. By proactively logging all weight-based transactions, managers have a fluid record that can be audited whenever necessary, thus reducing the risk of compliance-related penalties or operational downtime.
Conclusion
Accurate measurement in packaging remains a pivotal element of modern production lines. It ensures that businesses uphold operational consistency and meet the expectations of consumers and regulators. By leveraging technology suited to specific packaging environments, such as dynamic checkweighers or versatile bench scales, producers can safeguard product integrity and reduce costly errors.
We invite you to explore Sasco Africa’s comprehensive lineup of specialized equipment and services that could empower your packaging operations. Browse our range of scales and integrated solutions to discover the perfect tools for optimizing weight control, streamlining productivity, and upholding top-tier standards in your production line.